首钢250t/h步进梁式加热炉燃烧控制技术
1、加热工艺特点
2006年建成投产,设计产量为400万t/a,共配备3台结构相同的250t/h步进梁式加热炉,加热炉均热段上部采用平焰燃烧器,其余全部采用侧向调焰燃烧器供热。平焰燃烧器为CMC型(共24个),采用空煤气双旋流技术;侧燃烧器为低NO超长火焰(CMT型)燃烧器(共48个),侧燃烧器的超长火焰可覆盖整个炉宽。加热炉共设置6个炉温自动控制段,分别为第一加热段上、第二加热段上、均热段上、第一加热段下、第二加热段下、均热段下。为满足集中批量轧制和混合轧制生产的需要,加热炉需要经常转换生产模式,既有DHCR—CCR—DHCR(直接热装一冷装一直接热装)、HCR—CCR—HCR(间接热装一冷装一间接热装)不同装钢模式的转换,又有双相钢、高强合金钢及碳钢等不同钢种加热的转换。可以加热冷装坯料和不同人炉温度的热坯。
2燃烧控制技术
2.1平焰燃烧技术
均热段炉顶采用双旋流平焰燃烧技术,煤气由顶部引入燃烧器内管,经导流片使气流旋转,然后从燃烧器头部成一定角度喷出。空气由侧部进入燃烧器外管,按比例分两股流人燃烧器本体,经切向布置的导流孔后,旋转的气流在燃烧器头部与旋转的煤气气流混合燃烧,由于贴附效应,气流沿特殊设计的燃烧器砖内壁向四周铺展,从而形成贴附于炉顶的一层平焰。在均热段采用平焰燃烧技术,可有效调整板坯在长度方向的温度均匀性,减少头尾温差对轧制质量的影响。
2.2超长火焰燃烧技术
低NO超长火焰(CMT型)燃烧器用在加热炉的第一加热段上、下部;第二加热段上、下部;均热段下部。该技术为西玛高科最新的燃烧技术,采用二级燃烧机理,增长火焰长度,并降低炉内NO的产生。该技术最大特点是调节比大,在小流量燃烧状态下火焰长度长、刚性好,可以满足超宽板坯的加热要求。它采用特殊的燃烧供风(见图1)技术,中心风、一次风和二次风分别从三个平行的喷口喷出,通过调节一、二次风的比例调节火焰长度。
在投产试轧初期,由于火焰没有达到相应长度,板坯长度方向的温差偏大,影响了轧线的生产和试轧调整。通过反复测量数据,不断分析,得知火焰长度和刚度与燃烧器前空、煤气压力以及次风、二次风开启度有很大关系。一次风的开启度与火焰长度成反比,在烘炉或低温(≤80℃)时一次风一定要打开,确保与二次风的比例关系为3:7。燃烧器前中心风压力要保持稳定,一般保持在4000kPa左右。图2为火焰长度与助燃风的关系。
经实践证明,在燃烧器能力为额定能力的100%~40%时,火焰长度和刚度良好,炉膛宽度方向的温度均匀,板坯长度方向温度差小于3O℃。
2.3动态算法控制技术
为了保证在低负荷生产时炉宽方向的温度均匀,我们采用侧燃烧器动态算法控制技术,并取得了良好的使用效果。
2.3.1智能优化燃烧控制的原理和优势
顾名思义,智能优化燃烧控制是一种动态算法关闭侧燃烧器的燃烧方式,当加热炉低产时,各控制段需要的空、煤气流量相应降低,为了保证燃烧器火焰外形不变,各控制段需要关闭部分燃烧器,各控制段需要动态算法的燃烧器数量为:
n=int(n1-v段/2v燃烧器)
式中:n——各控制段每侧要关闭燃烧器数量
n1——各控制段每侧燃烧器数量
v段——各控制段燃料流量嘴
v燃烧器——侧燃烧器最大燃烧能力时燃料流量
燃烧器一旦工作,就处于高负荷状态(50%~100%),保证燃烧器火焰最长、最稳定,出炉板坯炉宽方向的温度均匀。当需要增加产量时,燃料消耗量增大,需要动态算法的燃烧器数量相应减少;当需要减小产量时,燃料消耗量减少,需要动态算法的燃烧器数量相应增加,控制图见图3。
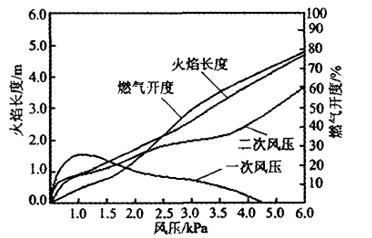
图2火焰长度与燃烧器嘴前压力关系
智能优化燃烧控制的主要优点为:
(1) 热效率高,大大降低能耗。
(2) 可提高炉宽方向温度场的均匀性。
(3) 通过在线调整实现炉内燃烧气氛的精确控制。
(4) 可提高燃烧器的负荷调节比。
(5) 系统简单可靠,造价低。
(6) 减少NO2的生成。
通过动态算法加热段燃烧器数量,控制不供热的热回收段的长度,尤其适应不锈钢加热工艺的需要,并有效回收烟气余热。
普通燃烧器的调节比一般为4左右,当燃烧器在高负荷工作时,燃气流速、火焰达不到要求,热效率急剧下降。普通燃烧器工作在负荷流量为50%以下时,上述稳各项指标距设计要求就有了较大的差距。智能优化燃烧控制则不然,无论在何种情况下,燃烧器只有两种工作状态,一种是高负荷(50%~100%)工作,另一种是不工作,当加热炉热负荷变化时,相应调整各段燃烧器工作状态,进行温度调节。所以采用智能优化燃烧可弥补燃烧器调节比低的缺陷,需要低产控制时仍能保证燃烧器工作在最侍燃烧状态。当燃烧器在高负荷工作时,燃气喷出速度快,周围形成负压,将大量炉内烟气吸入火焰根部,并进行充分搅拌混合,延长了燃气和空气接触时间,火焰长度以及高温区拉长,减少NO2的生成,增加了烟气与坯料的接触时间,从而提高了对流传热效率。另外,炉内烟气与燃气充分搅拌混合,使火焰温度与炉内烟气与燃气充分搅拌混合,使火焰温度与炉内烟气温度接近,提高炉内温度场的均匀性,减少高温火焰对坯料的直接热冲击,避免坯料局部过热、过烧,提高成品率,减少氧化烧损,有明显的效益。
燃烧气氛的调节是提高工业炉窑性能必不可少的一个环节,动态算法控制技术是在传统的连续燃烧控制上在燃烧器前增加关闭阀,通过开关各控制段侧燃烧器工作的数量来精确控制炉内的燃烧气氛。采用智能优化燃烧控制方式,只要加热炉产量恒定,高负荷工作的燃烧器数量就恒定,燃烧器前关闭阀工作频率比较低,因此系统工作稳定可靠。并可以根据系统的实际情况采取全自动控制或人工手动控制。
2.3.2智能优化燃烧控制在迁钢热轧加热炉上的应用
热轧加热炉在常规双交叉限幅控制六个供热段的基础上,辅以炉尾预热段,在第一加热段、第二加热段有低负荷自动关闭控制功能,即智能优化燃烧控制。在第一加热段上(J1)、下(J2)二段,两侧也各布置有五对燃烧器,其中各四对燃烧器带动态算法控制阀;均热段上加热24个平焰燃烧器及下加热的8个侧燃烧器都不能进行动态算法控制。
可根据热负荷情况,分别对J1、J2段及J3、J4段部分燃烧器进行关闭控制。当热负荷低于某一值Q1时,自动关闭一对燃烧器,当热负荷继续低于某一值Q2时,再自动关闭一对燃烧器(负荷低于50%必须进行关闭控制)。直到该段关闭,以保证燃烧器始终处在正常要求的工作负荷(100%~400%)下。当加热炉处于低负荷生产时,为了保护关闭的燃烧器不被炉膛高温烟气侵蚀氧化,我们只关闭燃烧器的煤气支管及一、二次风支管阀门,中心几管道始终保持全开状态,以高流速空气冷却燃烧器,燃烧器中心风的风量约占有燃烧器额定燃烧风量的3%~5%。
基于控制器双交叉限幅控制系统的动态算法控制技术,确保了低温供热段的燃烧稳定。在确保该炉区炉宽方向温度场均匀颁布的前提下,最大限度地优化了供热分配,可以灵活设定该区域的加热温度,尤其适合不锈钢板坯低温时缓慢加热的工艺要求。控制精度高,操作灵活,确保了不锈钢板坯的加热质量、同时提高了加热效率,降低了燃料消耗。
加热炉燃烧动态算法控制技术使加热炉二级燃烧最佳化控制得以实现,加热炉二级控制模型的控制思想是把加热炉的高温区段尽可能设定在加热炉出料端,让坯料在低温段吸收尽可能多的热量,最大限度降低排烟温度,提高加热炉的热效率,节约燃料。
智能优化燃烧控制技术根据加热炉二级系统温度设定值控制各控制段空、煤气流量,并根据流量的变化控制各加热段需要动态算法燃烧器的数量,而各加热段动态算法燃烧器的规律是从装料端向出料端依次动态算法,保持各加热段靠近出料端燃烧器高负荷燃烧,满足加热炉二级控制模型设定的温度曲线,使二级模型燃烧控制策略得以实现,并保证了烧钢质量。在加热炉低产或保温待轧时,燃烧器动态算法控制技术保持炉宽方向温度均匀性的同时,改善了操作环境,提高了炉底面积利用率和加热效率,降低了燃料消耗。智能优化燃烧作为一项新技术有着广阔的应用前景,在250t/h步进梁式加热炉上的成功应用,对提高产品质量、降低燃耗、减少污染将发挥重大作用,是工业炉行业燃烧自动控制的一次革新,将成为未来工业炉燃烧控制技术发展的一个方向。